Current transducers play a vital role in the smooth functioning of industrial automation. They are essential devices used for measuring and monitoring electric current in various industrial applications.
In this article, you will learn the significance of current transducers, their types, applications across different industries, technological advancements, challenges, and future outlook.
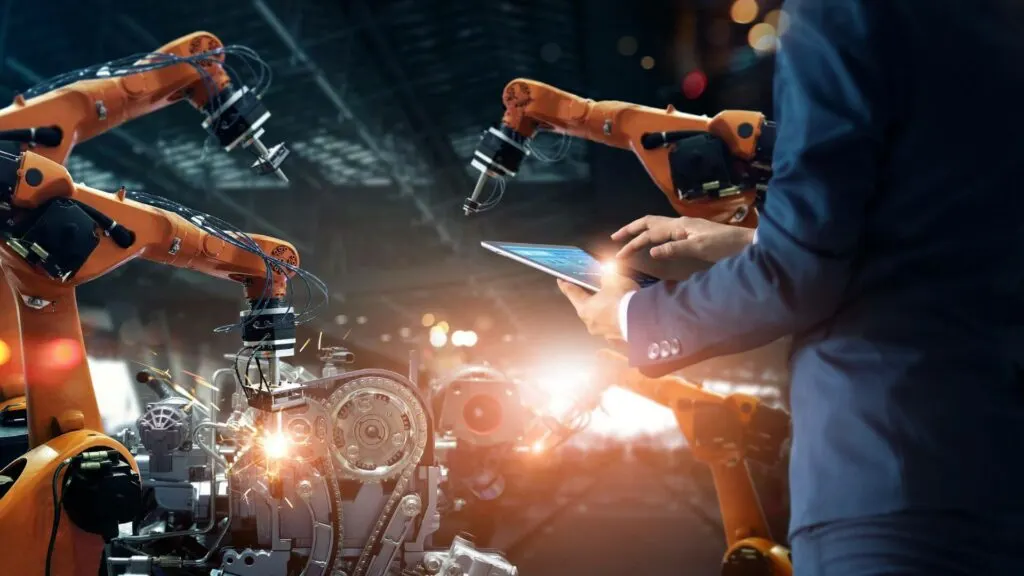
Understanding Current Transducers
The industry relies on current transducers to detect and convert electrical current into a proportional signal. Electrical system efficiency and safety depend on these devices, which come in many varieties.
Hall Effect Current Transducers
The Hall Effect Current Transducer operates based on the Hall Effect phenomenon discovered by Edwin Hall in 1879. This principle states that when a conductor carrying current is placed in a magnetic field perpendicular to the direction of current flow. A voltage is generated perpendicular to both the current and the magnetic field. In the context of current transducers, this voltage is proportional to the current being measured.
One key advantage of Hall Effect transducers is their ability to measure both AC and DC currents accurately. This versatility makes them suitable for a wide range of applications, including motor control, power monitoring, and battery management systems. Additionally, Hall Effect transducers offer high reliability and robustness, making them ideal for demanding industrial environments.
Rogowski Coil Current Transducers
Rogowski Coil Current Transducers utilize a flexible coil wound around the conductor whose current is being measured. When an alternating current flows through the conductor, it induces a voltage in the coil, which is then measured to determine the current magnitude. Unlike traditional current transformers, Rogowski coils do not have a magnetic core, making them more suitable for high-frequency and distorted current waveforms.
One notable advantage of Rogowski Coil transducers is their flexibility and ease of installation. The absence of a solid core allows them to be wrapped around irregularly shaped conductors, making them ideal for retrofitting existing systems or monitoring multiple conductors simultaneously. Also, their high-frequency response makes them well-suited for applications such as power quality monitoring and transient analysis.
Fluxgate Current Transducers
Fluxgate Current Transducers utilize a core made of ferromagnetic material that exhibits a nonlinear magnetic response to the applied current. By measuring changes in the magnetic flux within the core, these transducers can accurately determine the current passing through the conductor.
One of the key advantages of Fluxgate transducers is their high accuracy, particularly in measuring low currents. This makes them ideal for applications where precise current measurement is critical, such as in laboratory equipment and scientific instruments. Additionally, Fluxgate transducers offer excellent linearity and stability over a wide range of operating conditions, ensuring reliable performance in diverse environments.
Role of Current Transducers in Industrial Automation
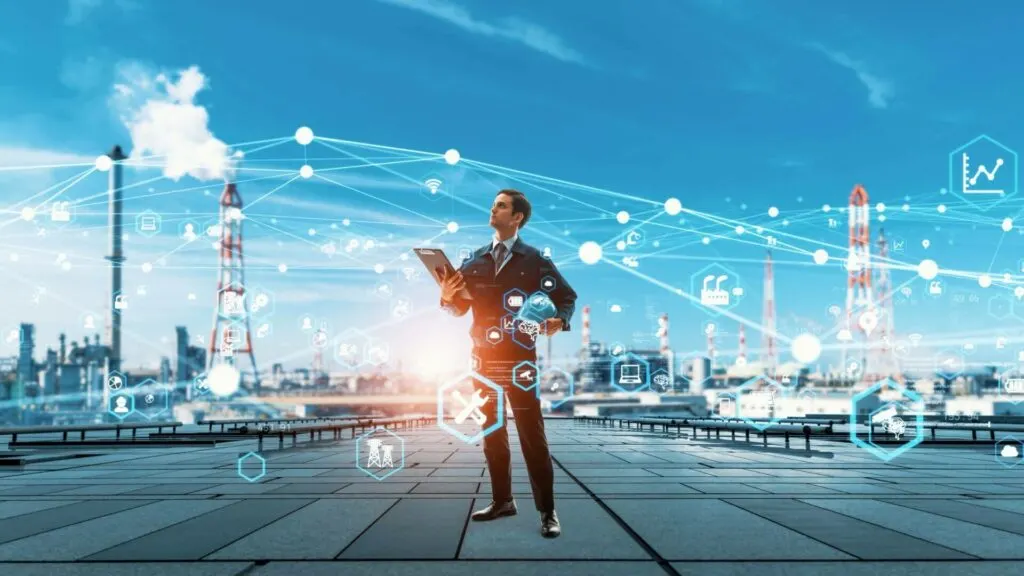
Current transducers are crucial in industrial automation due to their roles in monitoring, control, safety, energy optimization, and maintenance.
Real-Time Monitoring and Control
Current transducers offer continuous data on current flow, enabling precise adjustments for optimal performance. For example, in manufacturing, they monitor motor currents, allowing real-time control of speed and torque, and maintaining consistent product quality and production efficiency.
Safety Measures
Current transducers enhance safety by detecting overcurrent conditions that can cause equipment damage or fires. They monitor current levels to identify spikes or drops, triggering alarms or automatic shutdowns to prevent damage and ensure personnel safety. In electrical systems, they detect short circuits or ground faults, initiating protective measures to isolate faults and reduce risks.
Energy Optimization
Current transducers help optimize energy usage by providing detailed power consumption data. This data identifies areas of energy waste, enabling measures to reduce consumption. For instance, they monitor HVAC system power usage, allowing adjustments for optimal performance during different hours, reducing costs, and extending equipment lifespan.
Predictive Maintenance
Current transducers support predictive maintenance by detecting early signs of equipment wear or potential failures. For example, an increased current draw may indicate motor bearing wear. Identifying issues early allows proactive maintenance, preventing breakdowns and minimizing downtime, enhancing equipment reliability, and reducing maintenance costs.
Integration with Automation Systems
Current transducers integrate with programmable logic controllers (PLCs) and distributed control systems (DCS), enabling advanced control and monitoring. In an automated assembly line, they work with PLCs to adjust conveyor belts or robotic arms based on load conditions, ensuring efficient operation and dynamic response to production demands.
Environmental and Regulatory Compliance
Current transducers aid in complying with environmental regulations and standards by providing precise electrical consumption measurements and identifying inefficiencies. Accurate power usage monitoring supports energy management standards like ISO 50001 and helps in reporting energy savings, essential for certifications and sustainability incentives.
Current Transducer Technology Advances
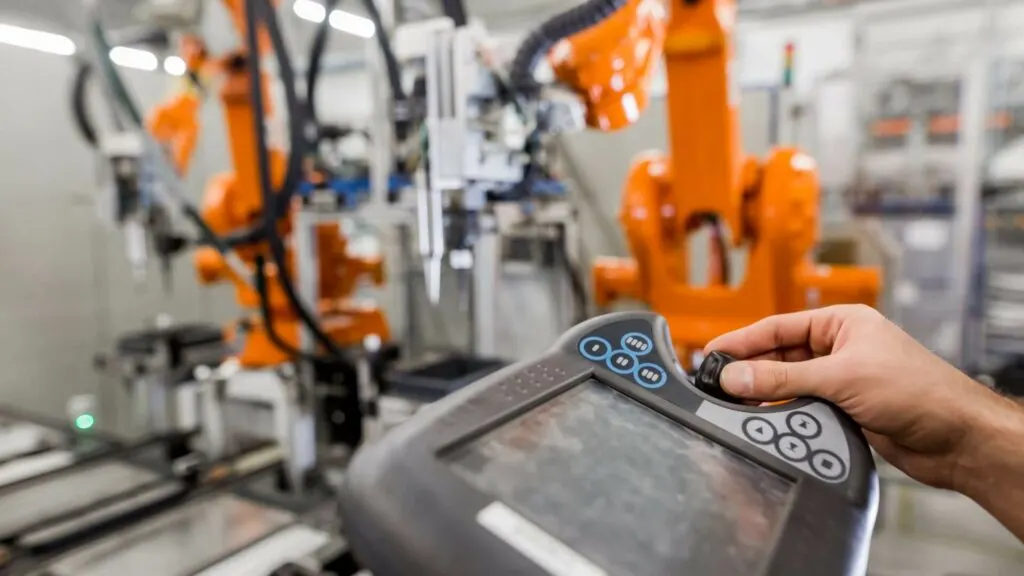
Transducer technology has developed, meeting the demanding needs of modern industrial applications.
Miniaturization, Integration
Miniaturization has produced compact current transducers. Innovative design methods like micro-electromechanical systems and semiconductor technologies enable smaller devices.
Compactness is essential for space-constrained applications like portable gadgets and dense industrial gear. PCB integration minimizes module count, improving system dependability and reducing connection failures.
Improved Precision and Sensitivity
Material science and sensor technology have greatly enhanced transducer accuracy and sensitivity. New magnetic core materials with reduced hysteresis and core losses and improved signal processing algorithms detect minute current variations.
Digital signal processing (DSP) improves noise filtering for reliable readings in electrically loud situations. Scientific research, medical diagnostics, and high-precision manufacturing require this.
Wireless Connectivity
Current transducer technology has advanced greatly with wireless communication. For remote monitoring and control, wireless transducers send real-time data to central monitoring systems or cloud platforms. These transducers use Zigbee, Wi-Fi, and Bluetooth for flexible deployment and IoT infrastructure integration. Wireless transducers provide real-time data for smart grid power usage and distribution management.
Smart Features
Smart current transducers have self-calibration and diagnostics. Built-in diagnostics let transducers monitor their performance and spot flaws before they fail. Transducers automatically self-calibrate to maintain accuracy in changing environments. These features save downtime and maintenance costs, improving system reliability.
The Energy Efficiency
Energy efficiency improvements have led to higher-performing transducers that use less power. Energy conservation is crucial for battery-powered applications and systems. For remote or inaccessible installations, low-power transducers with energy-harvesting methods can run for long durations without battery changes.
Customization and Application-Specific Designs
Improved customization allows manufacturers to create transducers tailored to industrial needs. Automotive transducers can resist high temperatures and vibrations, but medical transducers must be safe and accurate. This customization allows transducers to meet application-specific difficulties.
Current Transducers: Shaping the Future of Automation
Current transducers are indispensable components driving industrial automation. Their ability to accurately measure and monitor electric currents ensures the safety, efficiency, and reliability of industrial processes. With ongoing technological advancements and expanding applications, current transducers will continue to play a vital role in shaping the future of automation.
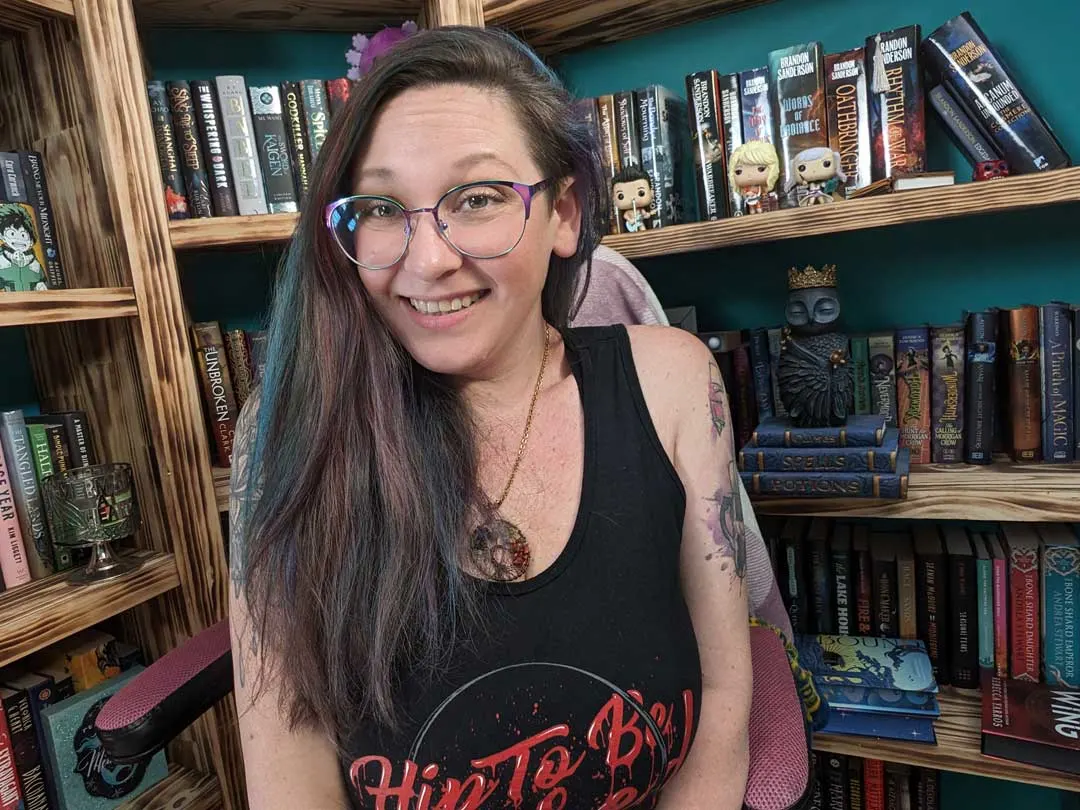
Jessi is the creative mind behind The Coffee Mom, a popular blog that combines parenting advice, travel tips, and a love for all things Disney. As a trusted Disney influencer and passionate storyteller, Jessi’s authentic insights and relatable content resonate with readers worldwide.