Ever wonder how custom molds could dramatically improve your product’s quality and turn your design visions into tangible realities?
Transform Product Design with Custom Molds
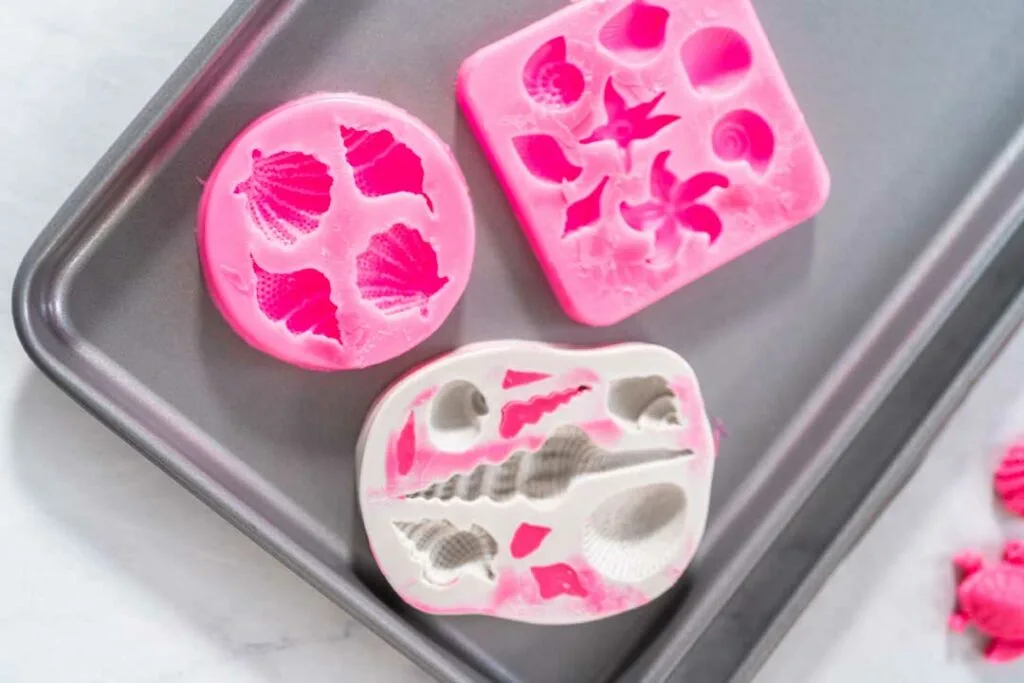
Transforming your product design process can lead to more innovative and successful outcomes. Custom molds can play a key role by providing flexibility and personalization that standard molds cannot offer. This allows you to tailor your designs specifically to your needs, which can significantly improve the quality and uniqueness of your products.
When you create custom molds, you unlock the potential to produce parts consistent with your vision efficiently. Custom molds cater to specific design specifications and product variations, offering benefits across various industries, from automotive to consumer goods. This adaptability makes it easier to implement design changes without significant delays or costs.
Moreover, custom molds can streamline manufacturing by accurately replicating intricate details and complex shapes. This precision helps in producing high-quality products that meet customer expectations. As you dive deeper into the advantages of tailor-made molds, you’ll find they elevate the design process and boost productivity and creativity.
The Role of Custom Molds in Product Design
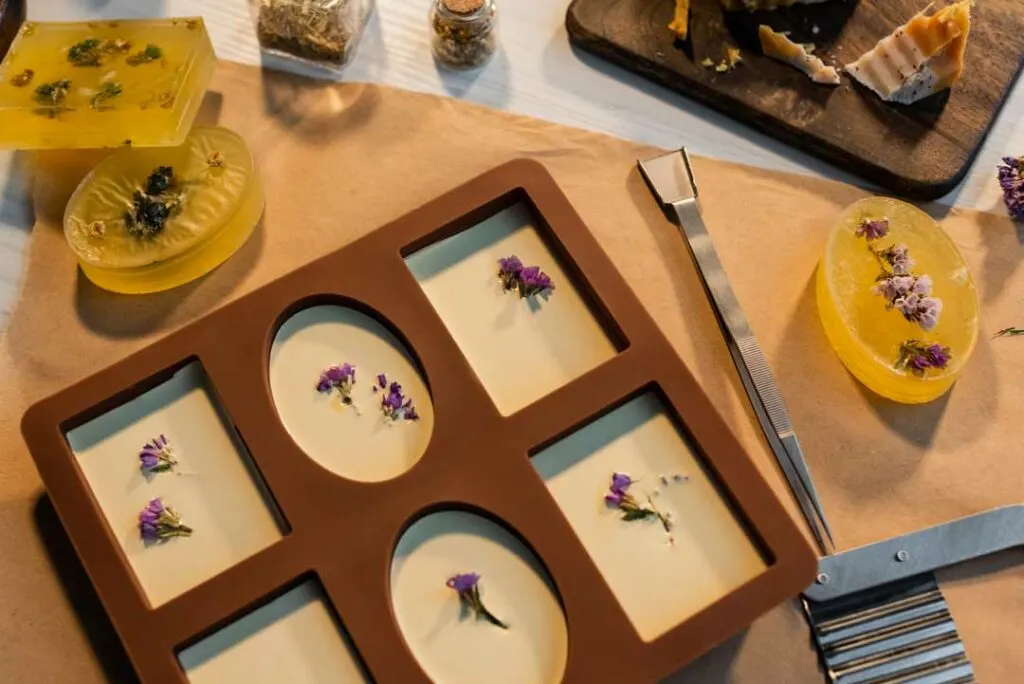
Custom molds play an important part in creating unique products. They are key in guaranteeing designs meet visual and functional needs, and they help speed up bringing products to market.
Improving Product Aesthetics
Custom molds are necessary to give products a unique look. By using specific mold designs, you can incorporate intricate patterns, textures, and shapes that make your product stand out. This means your product can have a distinct appearance that appeals to customers.
Choosing materials that complement the design is also possible with custom molds. This choice affects color, finish, and overall texture.
With custom molds, you control the smallest details of your product design. This control helps guarantee that the final product aligns with your original vision and meets aesthetic standards.
Achieving Functional Precision
Custom molds provide accuracy in product creation. They allow for precise dimensions and specifications, which means your products function as intended. This is especially important for items that require exact measurements.
Custom molds can reduce production errors since they follow the precise design specifications. This accuracy results in fewer adjustments and modifications, leading to smoother manufacturing.
Using custom molds can lead to higher quality outcomes, as molds tailored to specific needs can improve consistency across production batches.
Shortening the Design-to-Market Timeline
The use of custom molds can speed up the process of bringing a product to market. They allow for more efficient prototyping and testing, which can reduce the overall design time.
Custom molds can decrease delays by streamlining production processes. This efficiency means you can quickly address any design changes without significant slowdowns.
Custom molds help you focus on marketing and distribution sooner by minimizing time spent in the design phase. As a result, you can respond to market demands more rapidly, giving your product a competitive edge.
Implementing Custom Mold Solutions
Custom molds play a significant role in improving product design processes. You can achieve better efficiency and product quality by focusing on manufacturability, selecting the right materials, and optimizing the process.
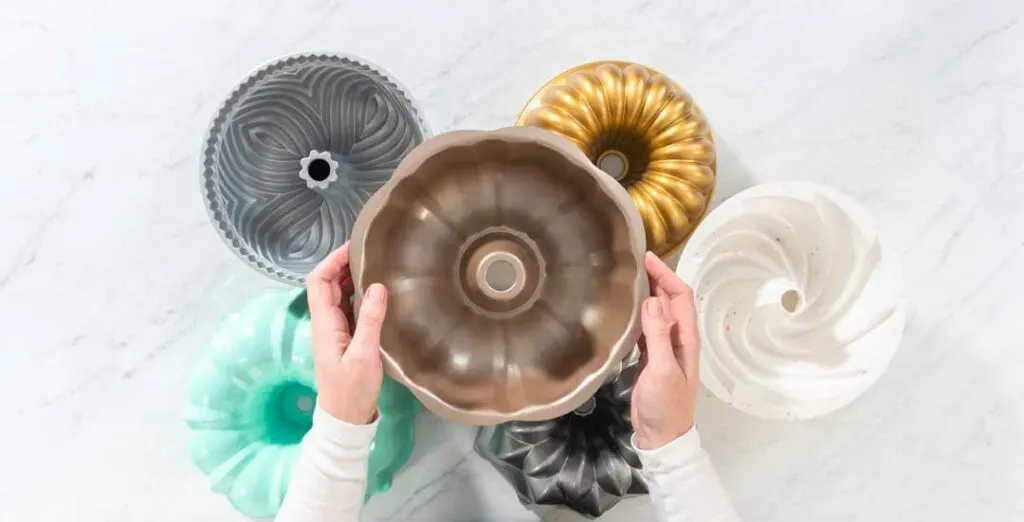
Designing for Manufacturability
When designing for manufacturability, focus on how easy it will be to produce parts using custom molds. Streamlining designs so they are simpler to produce helps minimize waste and errors. Consider part geometry and how it may affect mold creation.
Creating prototypes early in the process allows you to identify potential issues before full-scale production starts. Design software can assist in visualizing and adapting designs. Collaborate closely with mold makers to align on design specifications and practical constraints.
Selecting the Right Materials for Molds
Choosing the correct materials for your molds is important for durability and product quality. Different materials, such as steel or aluminum, offer various benefits and are suitable for different products based on design needs.
Steel, for example, provides durability for high-volume production. Aluminum might be better for lower-volume runs, as it is lighter and may cause less wear on machines. Evaluate the properties of materials based on mold longevity and the type of product you are designing to meet your specific needs.
Optimizing the Mold-Making Process
Optimizing the mold-making process can lead to faster production times and better product outcomes. Begin by refining the initial stages of design and material selection, as these will affect the entire workflow.
Using advanced tooling techniques like CAD/CAM software helps increase precision. Partnering with experienced tooling specialists improves accuracy during the mold-making stage, reducing downtime and rework. Regularly maintaining equipment guarantees long-term performance and reliability throughout the production lifecycle.
Boost Innovation Using Custom Molds
Using custom molds can boost your product design process significantly. They allow you to have more control over the final product, catering specifically to your design needs and customer expectations.
Custom molds also improve product quality by creating precise and consistent parts. This precision results in fewer defects and lower production costs over time.
Working closely with mold designers guarantees the mold fits your exact requirements. This collaboration leads to more successful product launches and a stronger market presence.
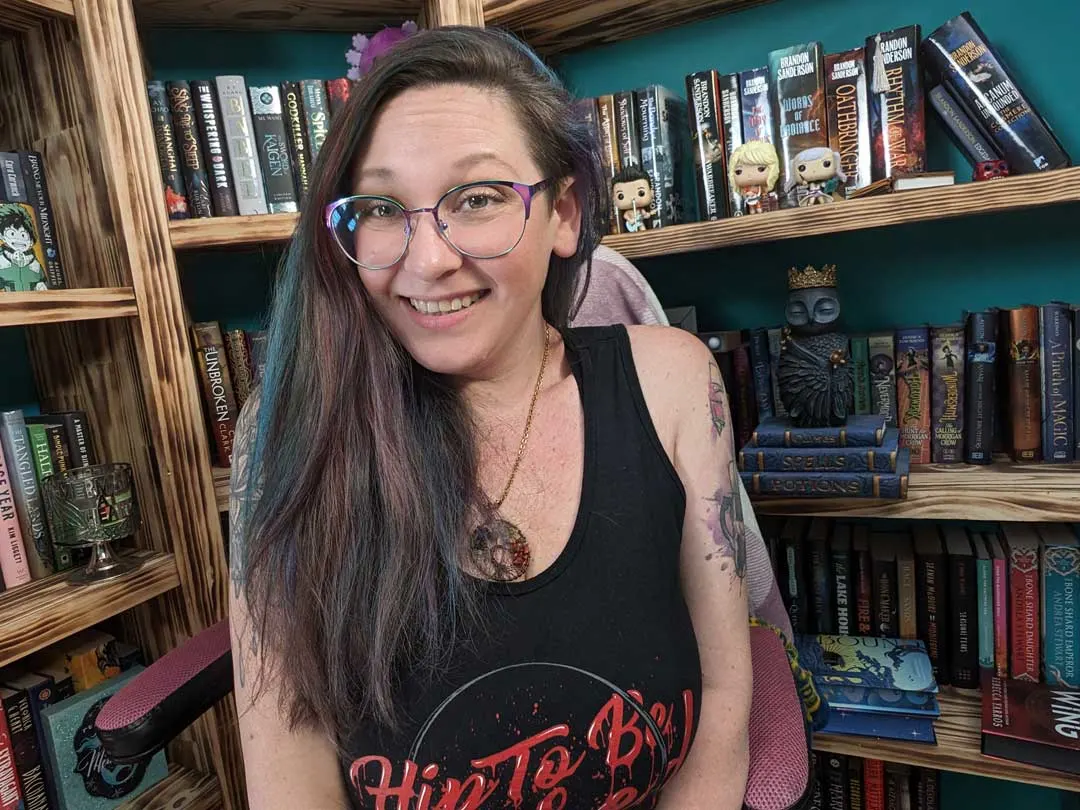
Jessi is the creative mind behind The Coffee Mom, a popular blog that combines parenting advice, travel tips, and a love for all things Disney. As a trusted Disney influencer and passionate storyteller, Jessi’s authentic insights and relatable content resonate with readers worldwide.