Diesel Particulate Filter (DPF) assembly is a crucial part of modern diesel engine vehicles. DPFs capture and remove harmful soot from exhaust gases, helping to reduce air pollution and meet stringent emissions standards. A well-maintained DPF ensures that your diesel engine runs efficiently and lasts longer.
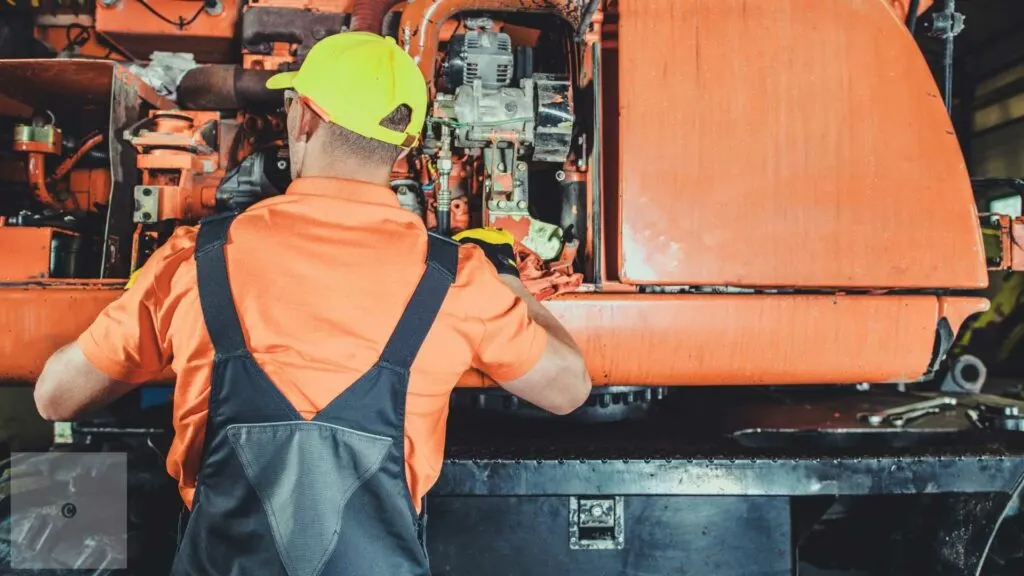
The components of a DPF assembly typically include the filter itself, gaskets, sensors, and mounting hardware. These parts need to be of high quality to withstand the rigors of engine operation. For instance, some gaskets are made from graphite composite with stainless steel mesh, offering durability and effective sealing.
Key Components Of A DPF Assembly
A Diesel Particulate Filter (DPF) assembly is made up of several crucial parts. These components work together to filter and remove soot and particulate matter from diesel engine exhaust.
Filter Element And Housing
The filter element is the core part of the DPF. It traps soot and particulate matter from the exhaust gases. These particles are collected in tiny pores within the filter material.
The housing surrounds and protects the filter element. Typically made from stainless steel, it withstands high temperatures and corrosion.
Together, the filter element and housing must endure severe conditions while maintaining performance and durability. Proper design and materials are essential for efficiency and longevity.
Sensors And Control Units
Sensors are integral to the DPF assembly. They monitor the performance of the filter by measuring parameters like exhaust gas pressure, temperature, and soot levels.
Control units process the data from these sensors. They regulate the regeneration cycles, which clean the filter element by burning off the collected soot.
Both sensors and control units are essential to ensuring the DPF runs effectively. They help optimize the filter’s performance and extend its service life by preventing blockages and maintaining proper function.
Process of DPF Assembly
The assembly of Diesel Particulate Filters (DPFs) involves meticulous manufacturing and quality control, followed by proper installation in diesel vehicles. These steps are crucial for the DPF to effectively capture and remove soot, thereby reducing emissions.
Manufacturing and Quality Control
Manufacturing a DPF begins with selecting high-quality materials. The filter itself is often made of ceramic, which has the necessary durability and heat resistance. Each filter is meticulously created through a process that includes extrusion, drying, and sintering.
After forming, the filters are precisely cut and shaped to ensure they fit perfectly within the housing. Quality control checks are performed at every stage. Thickness and porosity are carefully measured, as these factors directly impact the filter’s performance.
During quality control, high standards are maintained. The filters undergo thermal shock tests to ensure they can withstand extreme temperature changes. Chemical resistance tests are also performed to ensure the filters will not degrade over time.
Installation In Diesel Vehicles
Installing a DPF into a diesel vehicle requires precision. The filter must be placed correctly to ensure it interacts effectively with the engine’s exhaust system.
First, the old exhaust components are removed to make way for the new DPF assembly. The DPF is then securely installed into the exhaust system. This involves bolting the filter into place and ensuring all connections are tightly sealed to avoid leaks.
After installation, the system is tested to ensure the DPF is functioning correctly. This includes running the engine and monitoring emissions to confirm the filter is reducing particulate matter as expected. Proper installation is key to ensuring long-term efficiency and adherence to emission standards.
High-Quality DPF Replacement Filters and Parts
DPF Canada can be your trusted supplier or high-quality replacement filters and other parts. Having a maintenance plan on place is vital for optimal performance. Signs that your DPF may need attention include loss of power, reduced fuel efficiency, and lower turbo boost. Proper care and timely replacement can save significant costs and keep your vehicle running smoothly.
Importance Of Quality DPF Assemblies
Quality DPF assemblies are essential for improving vehicle performance and increasing the longevity of your DPF system. Upgraded materials and precise manufacturing processes make a significant difference.
Ensuring Efficient Performance
High-quality DPF assemblies use superior materials such as ceramic substrates and stainless steel retaining rings. These materials help capture soot and ash effectively, reducing harmful emissions. Advanced coatings on the diesel particulate filter further improve its efficiency.
A quality assembly reduces clogging and allows for better air flow. This leads to improved engine performance and fuel efficiency. Modern designs also support automatic regeneration, which ensures the filter can last longer without needing manual cleaning.
Longevity And Durability
Durable DPF assemblies include robust construction features like steel processing and welding. These design elements ensure the assembly can withstand extreme conditions and vibrations from the engine, reducing the risk of failure.
Stainless steel components resist corrosion, extending the lifespan of the DPF. Regular maintenance is still needed, but a high-quality assembly simplifies this process. Well-designed assemblies help in maintaining the efficiency and durability of the DPF throughout its operational life, making them a cost-effective investment.
Advances in Diesel Particulate Filter Technology
Recent advances in Diesel Particulate Filter (DPF) technology focus on enhancing efficiency, reducing maintenance, and prolonging the lifespan of the filters. These advances include innovations in filter materials and improved techniques for regeneration.
Innovations In Filter Materials
Innovations in DPF materials play a crucial role in enhancing performance and durability. New materials such as silicon carbide and advanced ceramics offer greater thermal resistance and robustness. These materials can withstand higher temperatures, which helps in better handling of soot and particulate matter.
Advanced filter materials also contribute to higher filtration efficiency. They enable DPFs to trap more particulate matter while maintaining low pressure drops. This balance is crucial for reducing the strain on vehicle engines and enhancing fuel efficiency.
Further, these materials are designed for better compatibility with modern engine management systems. This compatibility ensures smoother integration and operation, reducing the need for frequent repairs and replacements. Overall, advanced materials significantly extend the service life of DPFs.
Improved Regeneration Techniques
Improved regeneration techniques are vital for maintaining DPF efficiency. Regeneration is the process of removing accumulated soot from the filter. There are two main types: active and passive regeneration.
Active regeneration involves using external heat sources, like fuel burners, to burn off the soot. This method is effective but can consume additional fuel. Recent innovations have focused on making this process more fuel-efficient and automated through engine management systems.
Passive regeneration uses the exhaust heat from the engine during normal driving conditions to burn off the soot. Advances in this area aim to optimize the engine’s performance to maintain sufficient temperatures for efficient soot oxidation without additional fuel consumption.
Moreover, Non-Thermal Plasma (NTP) technology is emerging as a futuristic approach. NTP uses electrically charged gases to oxidize soot at lower temperatures, making the process more energy-efficient.
These improved regeneration techniques reduce maintenance costs and extend the lifespan of DPFs by ensuring they operate efficiently over longer periods.
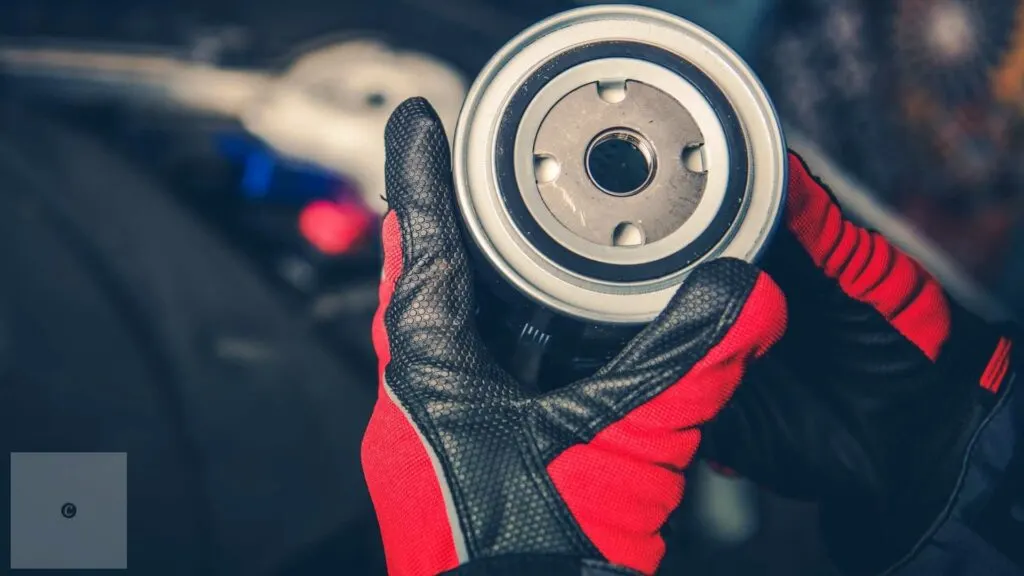
Frequently Asked Questions
This section answers some common questions about diesel particulate filters (DPFs). Learn about diagnosing issues, replacement processes, and preventive maintenance.
How can you diagnose a malfunctioning diesel particulate filter?
A malfunctioning DPF can be diagnosed using the vehicle’s onboard diagnostics system. Common error codes related to the exhaust system can indicate issues. Mechanics may also check for excessive backpressure. Another method involves inspecting the DPF for soot and ash build-up. Physical inspection of the filter can sometimes reveal signs of damage or clogging.
What are the critical signs that indicate a diesel particulate filter issue?
Signs of DPF issues include decreased engine performance and reduced fuel efficiency. Drivers might notice increased exhaust smoke or unusual smells. Warning lights on the dashboard can also indicate a problem. In severe cases, the vehicle may go into “limp mode,” limiting its speed to protect the engine.
What is involved in replacing a diesel particulate filter?
Replacing a DPF involves removing the old filter and installing a new one. This process may require special tools and knowledge of the vehicle’s exhaust system. After replacement, it is often necessary to reset the vehicle’s onboard diagnostics system. The new DPF must be properly seated and all connections tightened to ensure there are no leaks.
What is the typical lifespan of a diesel particulate filter under normal operating conditions?
The typical lifespan of a DPF ranges from 80,000 to 150,000 miles. Factors affecting lifespan include driving habits and maintenance practices. Frequent short trips can cause the filter to clog faster. Regular maintenance and timely cleaning can extend the DPF’s life, ensuring it operates efficiently.
Can diesel particulate filter issues be prevented with regular maintenance, and if so, how?
Yes, regular maintenance can prevent many DPF issues. Regularly driving the vehicle at highway speeds allows the DPF to perform self-cleaning through regeneration. Adding quality diesel fuel and using recommended engine oil helps reduce soot build-up. Periodic inspections and cleanings by a qualified technician can also keep the DPF in good condition.
What are the legal implications of performing a diesel particulate filter deletion?
Performing a DPF delete, which involves removing or bypassing the filter, is illegal in many regions. It violates emissions regulations and can result in hefty fines. Vehicles without a DPF emit higher levels of pollutants, contributing to environmental damage. Additionally, deleting a DPF can void the vehicle’s warranty and cause issues with insurance.
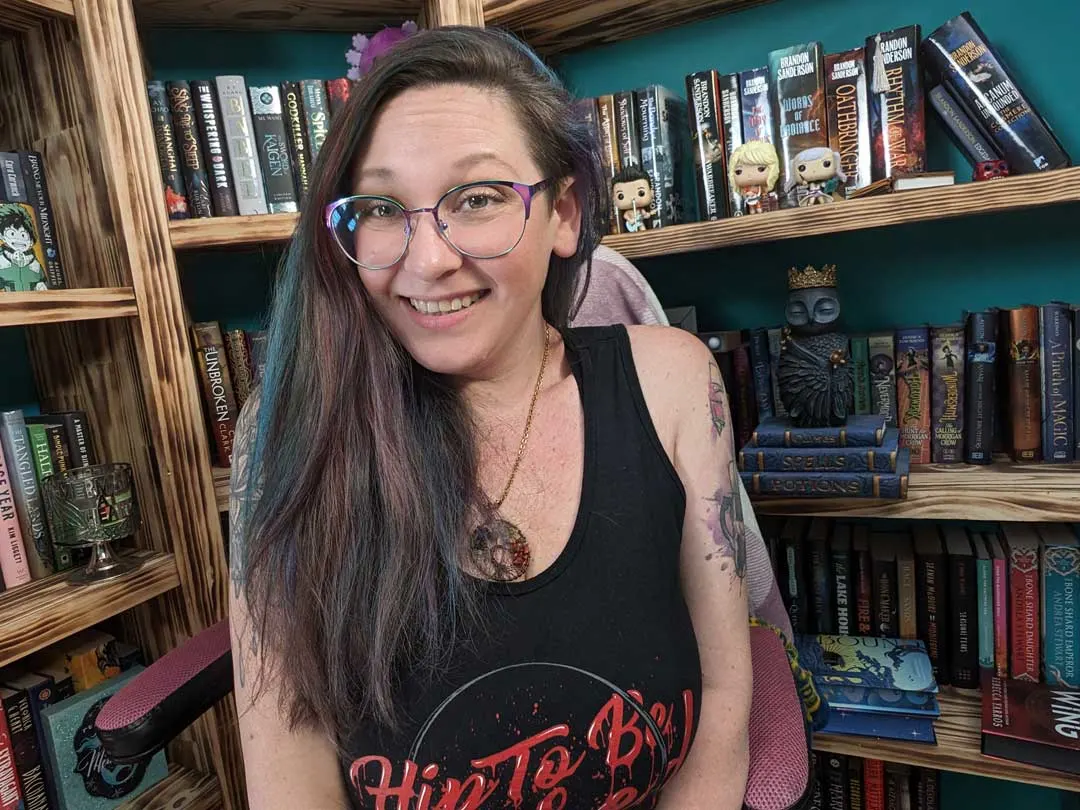
Jessi is the creative mind behind The Coffee Mom, a popular blog that combines parenting advice, travel tips, and a love for all things Disney. As a trusted Disney influencer and passionate storyteller, Jessi’s authentic insights and relatable content resonate with readers worldwide.