Your product or service needs to be of good quality in order to keep customers happy. A great way of maintaining high quality is to put in place quality controls. Below are some of the benefits of doing this and how you can implement quality control measures.
Why is quality control important?
There are several benefits to introducing quality control measures.
- Firstly, quality control promotes consistency. Customers can guarantee that they will get the same product or service each time. This ensures that return customers aren’t left unhappy because a product/service didn’t meet their expectations.
- Quality control allows mistakes to be identified early before they can do too much damage. It’s easier to undo mistakes at each step of the way than it is to go back later and fix them.
- Quality control can also help you to limit materials and costs. Without quality control measures, it’s harder to predict when materials will run out. You could also overspend money on your product, which could affect your profits.
- You can also implement quality control measures to make sure that your product or service is safe for the customer. For instance, it could be important to periodically test food in a factory to make sure that no batch has been contaminated.
- In some cases, quality control could be a legal obligation. For instance, bars are required by law to use specific spirit measures.
How to introduce quality control into your business
There are many ways in which you can control the quality of your work. Below are just some of the quality control measures that are worth putting in place.
Introduce protocol and precise measurements
Introducing a series of procedures to follow can make it easier to maintain a certain level of quality. For example, if you own a sandwich store and you want each sandwich to come out the same, you could consider putting in place basic rules such as cutting the bread in a specific way, always wearing gloves and only using ingredients sourced from specific suppliers.
Using measurements is very important for making sure that each product is the same. This could include using a specific amount of fillings per sandwich or cooking ingredients for a specific amount of time. You’ll need to decide which measurements are right for you – it could be worth experimenting a little to find the optimum amount of materials or time needed.
Train staff and create handbooks
There’s no point in having a protocol in place if you don’t train your employees on how to follow it. Make sure that every new staff member is taught the right steps to follow. Discourage any deviations from this protocol.
It’s worth exploring different ways to help employees memorize procedures. Some companies create acronyms in order to help staff remember certain series of steps. You could also place notes and posters in places to remind employees what to do.
Supplying a handbook could be useful when it comes to long series of procedures. Employees can then refer to this if they have any doubts as to what to do.
Monitor tasks and introduce quality control checks along the way
To help maintain quality, you should also consider periodically monitoring tasks to make sure that they are being performed to the right level. Obviously, you don’t want to be micromanaging your team – while new employees may need to be more regularly monitored, long-standing employees, should be left largely to their own devices to show that you trust them. That said, quality control checks are still important and you may want to occasionally check in to see what your loyal employees are doing.
There are all kinds of quality control checks that you can carry out. When it comes to important emails or written content, it could be worth having someone proofread them before they are sent or published. On a construction site, it could be important to carry out regular inspections on each new part of the build.
If problems are found, they need to be addressed and fixed there and then. Make sure that any fixes are permanent and not temporary, otherwise, you’ll be having to make another fix at a later stage. This is particularly important in tasks such as building software, which can result in tech debt if problems are continuously left unresolved or not fixed properly – there are ways in which you can measure tech debt to manage it. Making immediate fixes can be inconvenient sometimes, but it can prevent greater damage in the long run.
Automate quality control processes where possible
Too many manual routine procedures can make work boring. This is why such tasks should be automated where possible. Automation involves using machines or software to automatically carry out tasks. Not only can it be a way of reducing boredom for you and employees, but it could also make processes faster. Automating quality control also reduces the need for you or colleagues to manually carry out quality checks helping to free up human resources to work on other projects. It can also reduce the risk of mistakes as a result of human error.
Just what kind of quality control measures can be automated? A basic example could be using software tools to automatically check spelling and grammar or using automated machinery to periodically check the PH levels of a public swimming pool. In some cases, it may even be possible to automate fixes.
You should be careful of relying wholly on computers to carry out quality control as even they can sometimes make errors. A mixture of automated quality control and manual quality control is often the best solution for limiting mistakes and encouraging consistency.
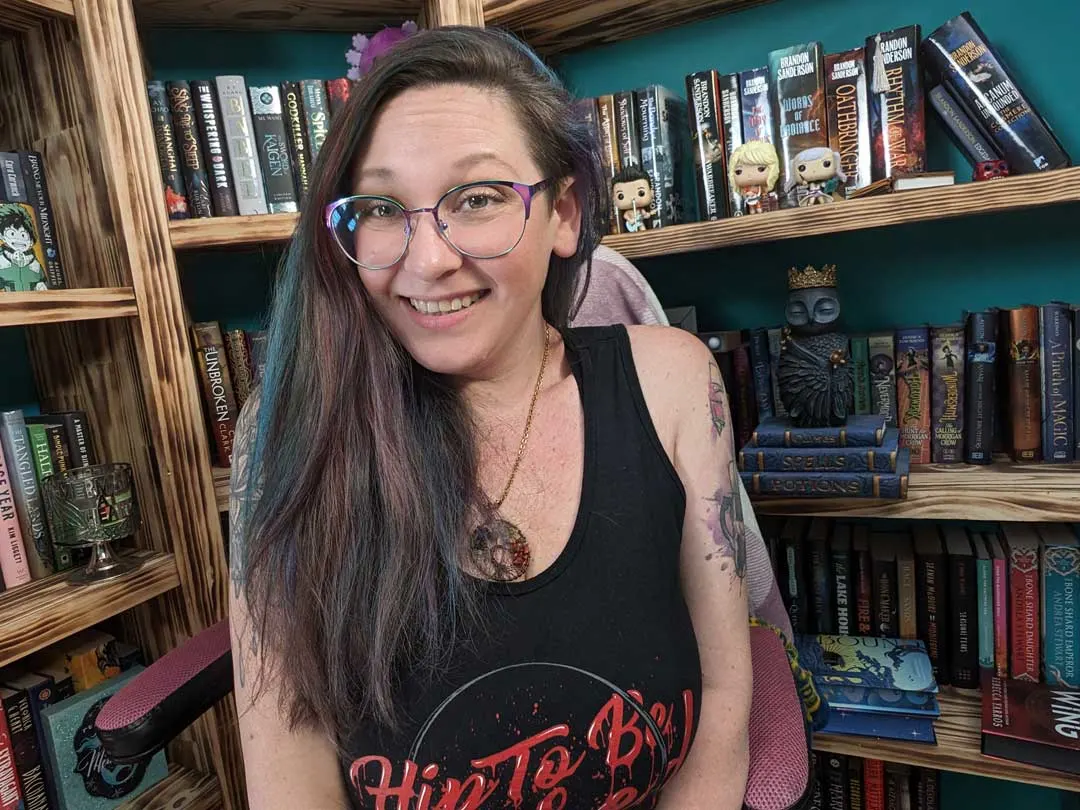
Jessi is the creative mind behind The Coffee Mom, a popular blog that combines parenting advice, travel tips, and a love for all things Disney. As a trusted Disney influencer and passionate storyteller, Jessi’s authentic insights and relatable content resonate with readers worldwide.